Maximizing Concrete Performance with Onsite Mixing
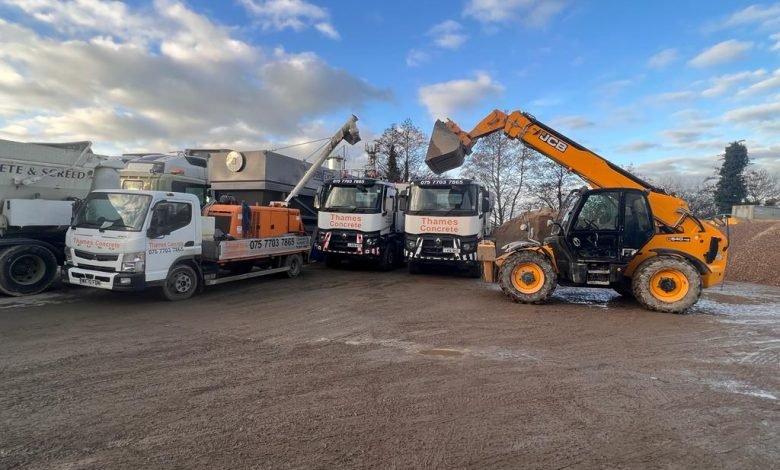
Concrete is a versatile and widely used construction material that can be used in various applications, including buildings, roads, bridges, and dams. The quality of concrete is critical to the performance and durability of structures. One way to improve the quality of concrete is through onsite mixing, which involves mixing the ingredients at the construction site instead of transporting ready-mixed concrete from a batch plant. Onsite mixed concrete can maximize the performance by providing greater control over the mix design, reducing transportation costs, and improving construction efficiency. This article discusses the benefits of onsite mixing and how it can help maximize concrete performance.
Benefits of Onsite Mixing to the Construction Project
Control over Mix Design
Onsite mixing allows for greater control over the mix design, which is critical to achieving the desired performance characteristics of concrete. Mix design involves selecting the type and proportion of materials used in concrete, including cement, aggregates, water, and admixtures. The mix design determines the strength, workability, and durability of the concrete. By mixing the ingredients onsite, contractors can adjust the mix design as needed to meet the specific requirements of the project. For example, a mix design that works well for a road might not be suitable for a bridge. Onsite mixing allows for greater flexibility in mix design, which can lead to better concrete performance.
Reduced Transportation Costs
Transporting ready-mixed concrete from a batch plant to the construction site can be costly, especially for projects located in remote or difficult-to-reach areas. The cost of transportation can significantly increase the overall project cost and reduce profitability. Onsite mixing can help reduce transportation costs by eliminating the need for ready-mixed concrete delivery. By mixing the ingredients onsite, contractors can minimize transportation costs, making it a more cost-effective option.
Improved Construction Efficiency
Onsite mixing can improve construction efficiency by reducing the time and effort required to transport ready-mixed concrete from a batch plant to the construction site. This can help speed up the construction process and reduce labor costs. Additionally, onsite mixing can allow contractors to adjust the mix design on the fly, which can help avoid delays caused by issues such as weather or unforeseen site conditions.
Maximizing Concrete Performance with Onsite Mixing
Proper Mixing Techniques
To maximize concrete performance with onsite mixing, it is important to use proper mixing techniques. Proper mixing involves ensuring that all the ingredients are thoroughly mixed, which helps ensure that the concrete has the desired strength, workability, and durability. The following are some tips for proper mixing:
- Use the correct mixing equipment: Using the right mixing equipment is critical to achieving a uniform mix. The equipment should be properly calibrated and maintained to ensure that it is functioning correctly.
- Use the correct mixing sequence: The sequence in which the ingredients are added can affect the quality of the mix. In general, the cement and aggregates should be mixed first, followed by the water and admixtures.
- Mix for the correct amount of time: The mixing time can affect the quality of the mix. Over-mixing or under-mixing can lead to issues such as a weak mix, excessive air content, or poor workability. The mixing time should be determined based on the mix design and the equipment being used.
- Monitor the temperature: The temperature of the concrete can affect its setting time and strength development. In hot weather, it may be necessary to cool the ingredients before mixing, while in cold weather, it may be necessary to heat the ingredients to ensure proper hydration.
Proper Curing Techniques
Proper curing is critical to maximizing concrete performance, regardless of whether it is mixed onsite or delivered from a batch plant. Curing involves keeping the concrete moist and at a consistent temperature to allow for proper hydration and strength development. The following are some tips for proper curing:
- Start curing as soon as possible: Curing should begin as soon as the concrete is placed to prevent rapid moisture loss and to promote hydration. Ideally, curing should begin within 30 minutes of placing the concrete.
- Keep the concrete moist: The concrete should be kept moist for at least seven days to promote proper hydration and strength development. This can be achieved by covering the concrete with a curing compound or by keeping it covered with a damp cloth or plastic sheeting. It is important to keep the concrete moist but not saturated, as excess moisture can lead to issues such as efflorescence or weakened concrete.
- Maintain a consistent temperature: The concrete should be kept at a consistent temperature during the curing process to promote proper hydration and strength development. In general, the temperature should be maintained between 50 and 90 degrees Fahrenheit, depending on the mix design and ambient conditions.
- Monitor the curing process: It is important to monitor the curing process to ensure that the concrete is curing properly. Signs of improper curing include cracking, surface discoloration, or reduced strength. If issues are detected, corrective action should be taken immediately to prevent further damage.
Also Read : Advantages using Water-Based Concrete
Conclusion
Onsite mixing can maximize concrete performance by providing greater control over the mix design, reducing transportation costs, and improving construction efficiency. To achieve maximum performance, proper mixing and curing techniques should be used. This includes using the correct mixing equipment, sequence, and time, as well as monitoring the temperature and curing process to ensure proper hydration and strength development. By following these guidelines, contractors can produce high-quality concrete that meets the specific requirements of the project, leading to better overall performance and durability.